Ölzustand inline überwachen: Optimierte Serviceplanung und Vermeidung von Maschinenschäden
-
Fluid.iO Sensor + Control GmbH & Co. KG
- 8 may. 2023
- 10
- 14.6 Minutos
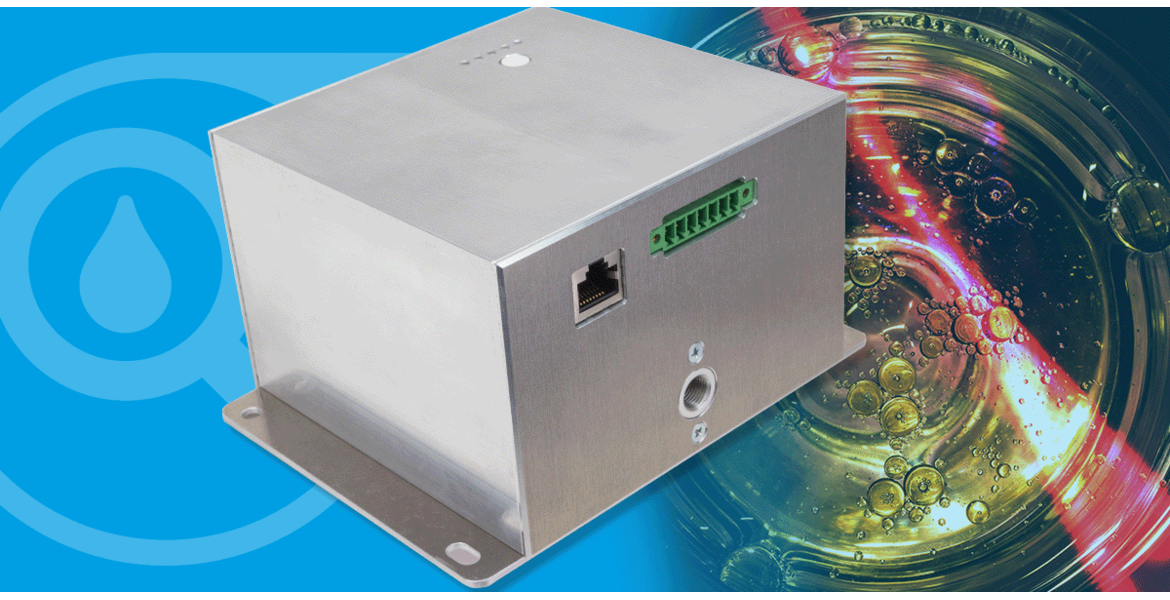
Überall dort, wo mechanische Energie mittels Generatoren in elektrische Energie umgewandelt wird, finden sich empfindliche Maschinenkomponenten und Anlagenteile, die dauerhaft mit Öl geschmiert werden müssen. Dies gewährleistet einen effizienten Betrieb und ein langes Maschinenleben.
Die Schmierung mit Öl verhindert, dass sich Maschinenteile berühren und abnutzen. Weitere wichtige Aufgaben des Öls sind die Abfuhr von Wärme und der Schutz von Korrosion.
Jedoch nimmt die Qualität des Öls im Laufe der Zeit ab, da sich die chemische Zusammensetzung des Schmierstoffes verändert, sodass dieser nicht mehr die gewünschten Eigenschaften besitzt, um die betreffende Maschine betreiben zu können. Solche Faktoren, die zur Verschlechterung des Ölzustandes führen können, sind unter anderem:
- Hohe Temperaturen in der Maschine
- Häufige Lastwechsel im Betrieb
- Verunreinigungen mit anderen Flüssigkeiten (z.B. Wasser)
- Verschleiß
Damit das verwendete Öl möglichst lange in der Maschine verbleiben kann, werden die Eigenschaften des Öls durch Additive verändert. Es ist jedoch festzustellen, dass trotz allem in den meisten Anwendungen ein regelmäßiger Austausch des Öls erfolgen muss. Dies verhindert Schäden an Maschinen und Anlagen und spart letztlich auch Kosten, da es nicht zum Stillstand der Maschine oder zu Wartungsaufwänden kommt. Wenn es gelingt, den Termin für den Ölwechsel optimal vorauszusagen und dahingehend auch Serviceeinsätze effizient zu planen, ergeben sich große Einsparpotenziale im Vergleich zu anderen Instandhaltungsstrategien.
Predictive Maintenance: Vorausschauende Wartung macht Service planbar
Bei der Wartung und Instandhaltung von Maschinen und Anlagen kommen sehr unterschiedliche Ansätze und Strategien zum Einsatz. Das grundlegende Ziel ist jedoch für jeden Anlagenbetreiber, stets die Leistungsfähigkeit der benötigten Ressourcen zu gewährleisten.
Die ausfallorientierte Instandhaltung, auch „Breakdown Maintenance“ genannt, birgt das große Risiko einer Maschinenstörung oder gar eines kapitalen Maschinenschadens. Da die Planung von Ressourcen wie Personal und Material für die Wartung nur schwer planbar ist, erfolgt diese reaktiv. Daraus ergeben sich wiederum entscheidende Nachteile hinsichtlich Ausfallzeiten und Servicekosten. Außerdem können ggf. sicherheitsrelevante Anforderungen an einzelne Anlagenkomponenten nicht eingehalten werden, weshalb diese Form der Instandhaltung bereits von anderen, vorausschauenderen Methoden (sog. Preventive Maintenance) abgelöst wurde.
Hierbei unterscheidet man in folgende Arten:
Die zeitbezogene Instandhaltung, orientiert sich an festen Serviceintervallen. So werden Filter, Dichtungen und Lager sowie das Öl in selbst definierten Zeitabständen ausgetauscht. Der Vorteil dieser Methode ist, dass die Intervalle auf Erfahrungswerten basieren und Verschleißteile daher im Sinne eines optimalen Maschinenzustands eher zu früh als zu spät ausgetauscht werden. Dadurch ist die Maschine optimal vor Ausfällen geschützt und Service- und Beschaffungsmaßnahmen können im Voraus geplant werden. Nachteilig ist diese Strategie hinsichtlich der Servicekosten, da möglicherweise Komponenten zu früh, zu häufig oder ohne Grund getauscht werden.
Mit der zustandsorientierten Instandhaltung kann der aktuelle Grad der Abnutzung eines Anlagenbauteils festgestellt und somit auf zukünftig notwendige Wartungsmaßnahmen geschlossen werden. Entsprechend werden kontinuierlich Ölproben aus einer Maschine entnommen und in einem Labor auf ihre Eigenschaften hin untersucht. Diese Ölzustandsanalyse im Labor erzeugt zwar im Vorfeld einer Wartung höhere Kosten, jedoch sind Wartungsmaßnahmen gut planbar und kritische Maschinenkomponenten können zum richtigen Zeitpunkt ausgetauscht werden. So kann stets ein optimaler Anlagenschutz gewährleistet werden.
Die prospektive Instandhaltungsstrategie, auch „Predictive Maintenance“ genannt, stellt eine gezielte Weiterentwicklung der zustandsabhängigen Instandhaltung dar. Deshalb verfolgen beide Strategien auch dieselben Ziele:
- Vermeidung von Maschinenschäden und Ausfallzeiten
- Optimale Ressourcen- und Serviceplanung
- Bestens für Fluide wie Öl geeignet
Die notwendigen Maßnahmen der Wartung ergeben sich aus dem qualitativen Zustand und einem vorhersagbaren (prospektiven) Abnutzungsverlauf. Die Vorhersage basiert auf der Auswertung von Sensordaten und daraus ermittelten Wartungsinformationen. Die Ermittlung eines optimalen Wartungszeitpunktes und die damit einhergehende Planungssicherheit führen zu attraktiven Kosteneinsparungen sowie einem schonenden Umgang mit Ressourcen.
Ausfallorientierte Instandhaltung |
Zeitbezogene Instandhaltung |
Zustandsorientierte Instandhaltung |
Prospektive Instandhaltung |
|
---|---|---|---|---|
Anlagenschutz | nein | ja | ja | ja |
Planbarkeit | nein | ja | ja | ja |
Abnutzungsvorrat | ja | nein | ja | ja |
Kosten | nein | nein | nein | ja |
Kontinuierliche Ölzustandsüberwachung zur Ermittlung der Ölqualität
Die Analyse des Ölzustandes liefert bereits frühzeitig Erkenntnisse über die Qualität des untersuchten Öls und damit auch über den Zustand einer Maschine. Gegenüber anderen Methoden ist der hierbei entstehende Zeitgewinn positiv hervorzuheben. Nachfolgende Grafik verdeutlicht den zeitlichen Verlauf der Entstehung von Maschinenschäden und welchen Vorteil die Überwachung der Ölchemie hierbei hat.
Abnutzung von Schmierstoffen durch Additive hinauszögern
Betrachtet man die Zusammensetzung von Ölen, so lässt sich feststellen, dass diese im Wesentlichen (75-99%) aus einem Grundöl, wie beispielsweise Mineral- oder Synthetikgrundöl, bestehen.
Der Rest des Grundöls (1-25%) sind Additive, welche dessen zentrale Leistungsaspekte optimieren, sodass das Endprodukt die für den gewünschten Anwendungszweck optimale Leistung abliefert.
Turbinen für Wasser, Dampf und Wind
Je nach Auslegung der Rotorblätter kommt es bei Windturbinen zu hohen Lasten und Schwingungen an den Lagern. Dadurch erhöht sich auch der Verschleiß, wodurch das Öl schneller altert. Je nach Standort kann außerdem Korrosion an den Lagern ein Alterungsfaktor sein. Dies betrifft unter anderem Turbinen in Küstennähe oder im Offshorebereich. Eine weitere Herausforderung bei der Auswahl des richtigen Öls speziell für Turbinen besteht darin, dass der Bildung von schädlichen Ablagerungen möglichst entgegengewirkt werden sollte. Daher muss gewährleistet sein, dass das Öl, auch wenn Wasser eindringt, seine Verschleißschutzeigenschaften beibehält. Ansonsten kann es zu einer Schäumung kommen, da eingeschlossene Luftbläschen aufgrund der hohen Druchflussmenge nur wenig Zeit haben aus dem Ölsumpf zu entweichen.
Bei Wasser- und Dampfturbinen ändern sich die Betriebsbedingungen hinsichtlich der Temperatur ständig. Dies ist auch dem Umstand geschuldetet, dass die Turbinen meist rund um die Uhr laufen. Durch Korrosion und Oxidation verschlechtert sich daher der Zustand des Öls stetig.
Stationäre Motoren
Öl für stationäre Motoren, wie z.B. Gasmotoren, wird durch die Verwendung von sauren Gasen völlig anders beansprucht. Schwierigkeiten, die hierbei häufig auftreten können, sind vor allem Ascheablagerungen in der Brennkammer sowie korrodierende Halogenverbindungen oder saure Substanzen im Gas. Dadurch wird die Lebensdauer des Öls stark verkürzt, weil der hohe Aschegehalt und der zunehmende Säurestress auf Dauer zu Verschleiß und Ablagerungen führen.
Transformatoren
Transformatoren sollen immer effizienter arbeiten, weswegen die Temperaturen, die Spannungen und die allgemeinen Belastungen, denen das Transformatorenöl ausgesetzt ist, stark zunehmen. Im Umkehrschluss führt das häufig zu einer übermäßigen Beanspruchung. Daraus resultiert die Notwendigkeit für Anlagenbetreiber das Grundöl mit Additiven zu modifizieren und so, wie bereits beschrieben, seine Eigenschaften zu verbessern. Beispielsweise kann durch den Einsatz eines verschleißhemmenden Additives ein Abrieb durch zwei aufeinandertreffende metallische Oberflächen vermieden und Ventilklemmung vorgebeugt werden. Gleiches trifft auf die Bewältigung von Rußablagerungen und anderen Verunreinigungen zu. Wird der Anteil an Antioxidantien im Öl erhöht, so kann das Öl außerdem auch höheren Belastungen standhalten; Korrosion wird somit verhindert und einem Abreißen des Schmierfilms wird entgegengewirkt.
Messverfahren zur Ermittlung typischer Ölzustandsparameter
Mithilfe modernster Messverfahren und -geräte können im Labor wichtige Kenngrößen zur Feststellung des Ölzustands (z.B. Oxidation, Nitration, Wassergehalt etc.) bestimmt werden. Einige davon möchten wir im Folgenden etwas näher erläutern.
Das ICP-Verfahren als Methode der Atomspektroskopie dient zum Nachweis von Verschleißmetallen, Verunreinigungen und Additiven im Öl. Diese Methode basiert darauf, dass angeregte Atome eine entsprechende elektromagnetische Strahlung aussenden, die anschließend Aufschluss über die chemische Zusammensetzung des Gebrauchtöls gibt.
Das Viskosimeter wird zur Bestimmung der Viskosität eingesetzt, um den Widerstand einer Flüssigkeit gegen eine erzwungene Bewegung feststellen zu können. So ist es möglich eine Aussage über das Fließverhalten von flüssigen Stoffen, in unserem Beispiel speziell von Öl, zu treffen. Mehr über dieses Messverfahren sowie unser Viskosimeter erfahren Sie hier: FluidIX Lub-VDT
Die FTIR-Spektroskopie gehört zu den Infrarotspektroskopien und wird in der Ölzustandsanalyse verstärkt zur Bestimmung der Veränderungen eines Gebrauchtöls im Gegensatz zum Frischöl eingesetzt. Dadurch, dass verschiedene Moleküle, je nach Ölsorte, Infrarotlicht bei bestimmten Wellenlängen unterschiedlich stark absorbieren, kann dieser Vergleich stattfinden. Eine Signalverschiebung innerhalb von spektralen Banden zeigt dann an wie stark das Öl gealtert ist.
Vorteile unseres Ölzustandssensors FluidIX Lub-6
Mit dem neuartigen Ölzustandssensor FluidIX Lub-6 zur direkten Integration in eine Maschine bzw. Anlage eröffnet die ZILA GmbH für Anlagenbetreiber eine Vielzahl neuer Möglichkeiten. Das Aufzeichnen mehrerer Messwerte sowie das komfortable Einstellen von Grenzwerten ermöglichen eine kontinuierliche Überwachung des Ölzustands. Mit welcher Technologie dies realisierbar ist und welche weiteren Vorteile unser Sensor im Bezug auf Bedienung und die Wirtschaftlichkeit einer Anlage bietet erfahren Sie jetzt.
Die Technologie
Der FluidIX Lub-6 arbeitet auf Basis der NDIR-Technologie (nicht-dispersive Infrarottechnologie), welche vom Prinzip her ähnlich wie die bereits beschriebene FTIR-Spektroskopie funktioniert. Die Ölprobe wird ebenfalls mit infraroter Strahlung durchleuchtet; der entscheidende Vorteil gegenüber der FTIR-Spektroskopie ist jedoch, dass nur ein Teil des IR-Spektrums aufgezeichnet wird. So werden mithilfe von Wellenlängenfiltern nur diejenigen Bereiche betrachtet, die einen Alterungseffekt aufweisen.
Vorausschauender Ölwechsel für Maschinen und Anlagen
In der Vergangenheit wurde häufig die ausfallorientierte Instandhaltungsstrategie verfolgt, bei der Stillstands- und Ausfallzeiten stets unumgänglich waren. Von diesem Ansatz ist man heute fast komplett weggekommen, da Ausfallzeiten aus Gründen der Wirtschaftlichkeit vorgebeugt werden sollen. Die NDIR-Technologie unterstützt diesen Prozess und stellt eine komprimiertere Variante der FTIR-Spektroskopie dar. Aufgrund dieser innovativen Technologie kann der Sensor als Inline-Anwendung realisiert werden und eignet sich folglich perfekt für die Echtzeitüberwachung des Ölzustands.
Der Sensor liefert permanent aussagekräftige, mit Laborqualität vergleichbare Informationen über verschiedene Parameter (z.B. Oxidation, Wassergehalt, Additivgehalt (Phenole) usw.). Dadurch wird die Ermittlung des optimalen Zeitpunkts für einen Ölwechsel in einer Maschine oder Anlage ermöglicht und zum anderen für eine optimale Nutzung des Abnutzungsvorrats gesorgt. Der FluidIX Lub-6 trägt somit also essenziell zur einer organisierten, planbaren Serviceplanung und Instandhaltung bei.
Schnelle Integration des FluidIX Lub-6 in bestehende Anlagen
Die folgende Abbildung zeigt die einfache Integration unseres Sensors in den Ölkreislauf einer Anlage. Eine Anbindung an die Maschinensteuerung kann über digitale Signale oder Modbus TCP erfolgen.
Komfortable Inbetriebnahme und Bedienung über Webinterface
Die Inbetriebnahme und Bedienung des Ölzustandssensor FluidIX Lub-6 erfolgen bequem über eine grafische Benutzeroberfläche, welche an einem Computer aufrufbar ist. Über dieses Webinterface können alle Konfigurationen und Sensoreinstellungen, wie beispielsweise das Einstellen von Grenzwerten und Messintervallzeiten, vorgenommen werden. Ebenso ist es möglich, die Messwerte grafisch darzustellen, woraus dann in weiterer Folge bereits frühzeitig ein Trendverlauf sowie entsprechende Instandhaltungsmaßnahmen abgeleitet werden können. Eine weitere Komfortfunktion ist, dass der Sensor als Datenlogger fungiert, das heißt es können auch zu einem späteren Zeitpunkt noch Informationen über die vorherige Konfiguration des Sensors abgerufen werden.
Fazit
Mit unserem Ölzustandssensor FluidIX Lub-6 kann der Service- und Wartungsaufwand deutlich reduziert und die Lebensdauer einer Anlage verlängert werden.
Ebenso werden Stillstands-, Beschaffungs- und Entsorgungskosten durch den Einsatz des FluidIX Lub-6 stets gering gehalten.
Sollten Sie mehr Informationen zu diesem Produkt benötigen, finden Sie diese auf der folgenden Produktseite: Ölzustandssensor FluidIX Lub-6

FluidIX Lub-6
Sensor de condición de aceite apto para instalación en línea, basado en una célula de medición por infrarrojos multicanal, para la supervisión permanente del estado del aceite y la prevenció
Basado en la tecnología infrarroja no dispersiva (NDIR), ZILA GmbH ha desarrollado un sistema de medición en línea que supervisa de forma permanente el estado del aceite directamente en el sistema. El sistema de medición óptico consiste en una célula de medición por infrarrojos multicanal con la electrónica y los periféricos asociados.
¡Nuestros ingenieros de aplicaciones le asesoran personal, completa y profesionalmente!
¡Póngase en contacto con nosotros por teléfono o por escrito!