Detection of leaking conductive and non-conductive operating materials with the aid of leakage sensors
-
Fluid.iO Sensor + Control GmbH & Co. KG
- Jan 3, 2024
- 54
- 4.1 minutes
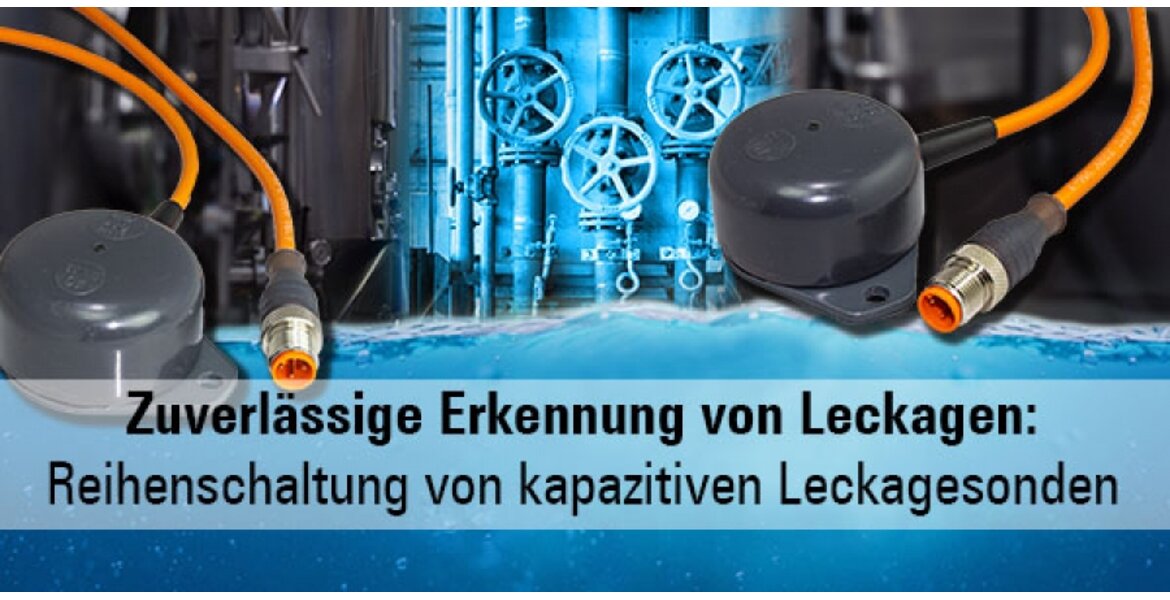
Leakage sensors for the rapid detection of leaking operating fluids and other conductive or non-conductive liquids in large production halls and manufacturing plants.
Liquid escaping from leaks causes damage to machinery & is a danger to people
Leaks are an annoying and, in most cases, unavoidable issue in all areas of industry. They can occur in systems, pipes, fittings or heating systems and cause damage to machinery, building structures or become a danger to people. The list of leaking liquids ranges from process water, cooling lubricants and oils to dangerous acids and alkalis. If a leak is not recognised or only recognised after a long period of time, the resulting damage can only be remedied with a high level of financial and personnel expenditure and costs.
For the safe and early detection of these leaks, E.L.B. Füllstandsgeräte GmbH has been offering a wide range of customised solutions for over 40 years, which can be tailored precisely to the conditions of the customer's application.
The compact floor sensors in particular, which can also be arranged in a series connection, are ideal for leakage detection in large production halls or manufacturing plants.
Ultrapure water in the pharmaceutical industry
In the pharmaceutical industry, ultrapure water is an important basis for many processes. Ultrapure water is free from foreign substances and is therefore ideal for analytical purposes. In pharmaceutical production, it is used for product preparations or final formulations. Ultrapure water is also used for quality control in pharmaceutical production. In the dissolution test, the release of a substance is analysed, i.e. when a solid form becomes a dissolved form under simulated physiological conditions. The industry generally uses ultrapure water to produce this physiological medium. Ultrapure water can also be used to clean systems or system components. In order to meet the demand for ultrapure water in pharmaceutical plants, there are ultrapure water systems on site that provide sufficient quantities of the medium using membrane technologies (reverse osmosis), nanofiltration or distillation processes.
Early detection of leaks in the ultrapure water network
Time and again, leaks can occur during storage, at extraction points or during the distribution of ultrapure water through a pipe network due to overfilling, corrosion, outdated seals or carelessness. In addition to the economic loss of the expensively treated ultrapure water, this can also lead to damage to the surrounding building fabric, neighbouring systems or the product itself. In order to avoid or minimise such damage, early detection and localisation of the leak is very important. The size of the ultrapure water network (storage areas, widely distributed pipework, numerous extraction points) within a production facility poses a particular challenge, as the leak can occur at several points at the same time.
Leakage detection on large surfaces through series connection of capacitive point sensors
A variety of different measuring principles are available on the market for the detection of leaking liquids. When selecting a suitable measuring method, the medium to be detected must be taken into account in addition to external conditions such as pressure, temperature and the installation situation on site. Due to the large surface area over which the liquid can spread in production facilities, float solutions in which a float with a magnet is propelled through the liquid and activates an alarm contact are not a suitable solution. Reaching the response height of the float requires a large liquid leakage. For the detection of escaping ultrapure water, it must also be taken into account that the medium only has a very low electrical conductivity, which is why conductive level measurement is also unsuitable.
For these reasons, we recommend capacitive measurement, which is suitable for conductive and non-conductive media. To ensure fast detection of the leakage, the sensor was designed as a so-called floor sensor.
The electric field created by the sensor is generated directly on the underside of the housing. Even a small film of liquid on the surface is therefore sufficient to change this electric field, which in turn is detected by the sensor. An alarm or automatic interruption of the liquid supply is then triggered by means of a potential-free output contact. An outstanding feature of this capacitive floor sensor is the simple linking of several sensors in a series connection. This means that large areas can be monitored selectively and analysed at a central unit.
Advantages for system operators through capacitive leakage probes
By simply linking several leakage probes, the number of sensors can be individually adapted to the conditions on site. Critical points are monitored more sensitively with several sensors, while less critical points are monitored with just one or two sensors. The capacitive measuring principle in conjunction with the flat design of the leakage sensor ensures fast and reliable detection even at low liquid levels. If a leak is detected, an alarm can be sent immediately to a central evaluation unit via the signalling contact or the automatic supply of liquid to the tank or pipework can be stopped. This minimises consequential damage and saves costs for time-consuming cleaning work or repairs.
In addition to the KL25P capacitive floor sensor, other compact designs are also available for various applications. Fixed rod versions such as type KL25F, for example, are ideal for lateral installation in a leakage tray, whereas the suspended version type KL25H is ideal for installations in underground areas or leakage shafts. The capacitive leakage probes are approved by the DIBt (German Institute for Building Technology) for the detection of leaking water-polluting liquids and are therefore suitable for a wide range of media. Even in highly aggressive media, a long service life can be guaranteed by choosing the right plastic material.
Our application engineers advise you personally, comprehensively and professionally!
Simply contact us by phone or e-mail!